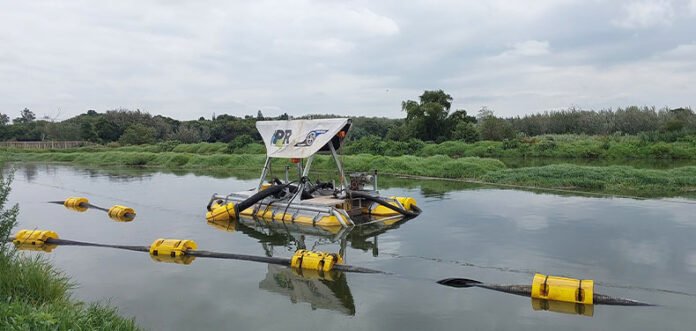
Developed by local pump and dredging expert IPR, the SlurrySucker dredging system recently provided the ideal solution for getting the emergency water dams at a Gauteng wastewater treatment plant back to optimal condition.
Warren Spann, Business Development Manager at IPR, explains that the emergency dams had filled with sludge over time, and were presenting an operational risk to the plant. Dredging the dams with hydraulic excavators was not effective for a number of reasons, and the manual removal of sludge in trucks caused environmental challenges. The dams are vital sources of additional water for the treatment plant during times when insufficient volumes are flowing into the facility.
“IPR was contracted to conduct the dredging of these emergency water dams, and we put our new generation SlurrySucker Maxi onto the job,” says Spann. “This powerful dredging system is equipped with three Toyo K30 heavy-duty submersible slurry pumps, and was able to remove 50 dry tonnes per hour.”
Importantly, these specialised heavy duty 22kW Toyo pumps are capable of dealing with the wide variety of solids that accompany the wastewater to the plant including rags, nappies and even pillows. The pumps’ capacity allowed them to pump the sludge through 450 metres of pipeline on this contract, without the need for inline boosting.
Mounted on a purpose-designed pontoon, the SlurrySucker Maxi was drawn from across the 250 m long dams using ropes and a winching system. The operation was managed through remote controls in the hands of a trained and experienced technician, ensuring optimum safety.
“There were also two Atlas Copco WEDA D70H jetting pumps on the pontoon, to help stir up the sediment in the dams,” he says. “The first pump jets water down to the dredge head to agitate compacted sludge on the bottom of the dam, while the second pump jets water into sludge that is near – or even protruding from – the surface of the water. The latter is necessary as the pontoon needs 350 to 400 mm of water on which to float.”
To ensure that the discharge from the dredging activity complied with environmental standards, the dredged material was pumped into large dewatering bags. Each bag held 25,000 tonnes of material, and measured 30 m in circumference and was 60 m long.
These bags allowed water to weep out into a catchment pond, and IPR added a flocculant to the pipeline to help the solid materials to settle out. This strategy helped the wastewater plant to conserve water, as the filtrate was pumped back to the plant for re-use. The added flocculant in the filtrate assisted the plant further by contributing to the levels of flocculant that the plant would be adding as part of its normal process.
Lime was used to reduce the odour from the dewatering bags, giving the customer various options related to removing the material later including the provision of activated sludge to the agricultural sector.
“An added advantage of our dredging technique is that all our equipment is electrically powered, so it operates with hardly any noise,” says Spann. “This is in stark contrast to heavy mechanical equipment, and meant that we did not disturb the neighbouring residential estate.”
He adds that IPR’s advanced control panels on the SlurrySucker ensured that the power would trip if any oversize material threatened to damage the pumps. The panels convey an error message to the operators, so they can resolve the issue and return the system to work without risking any further harm to the equipment.